Jidoka
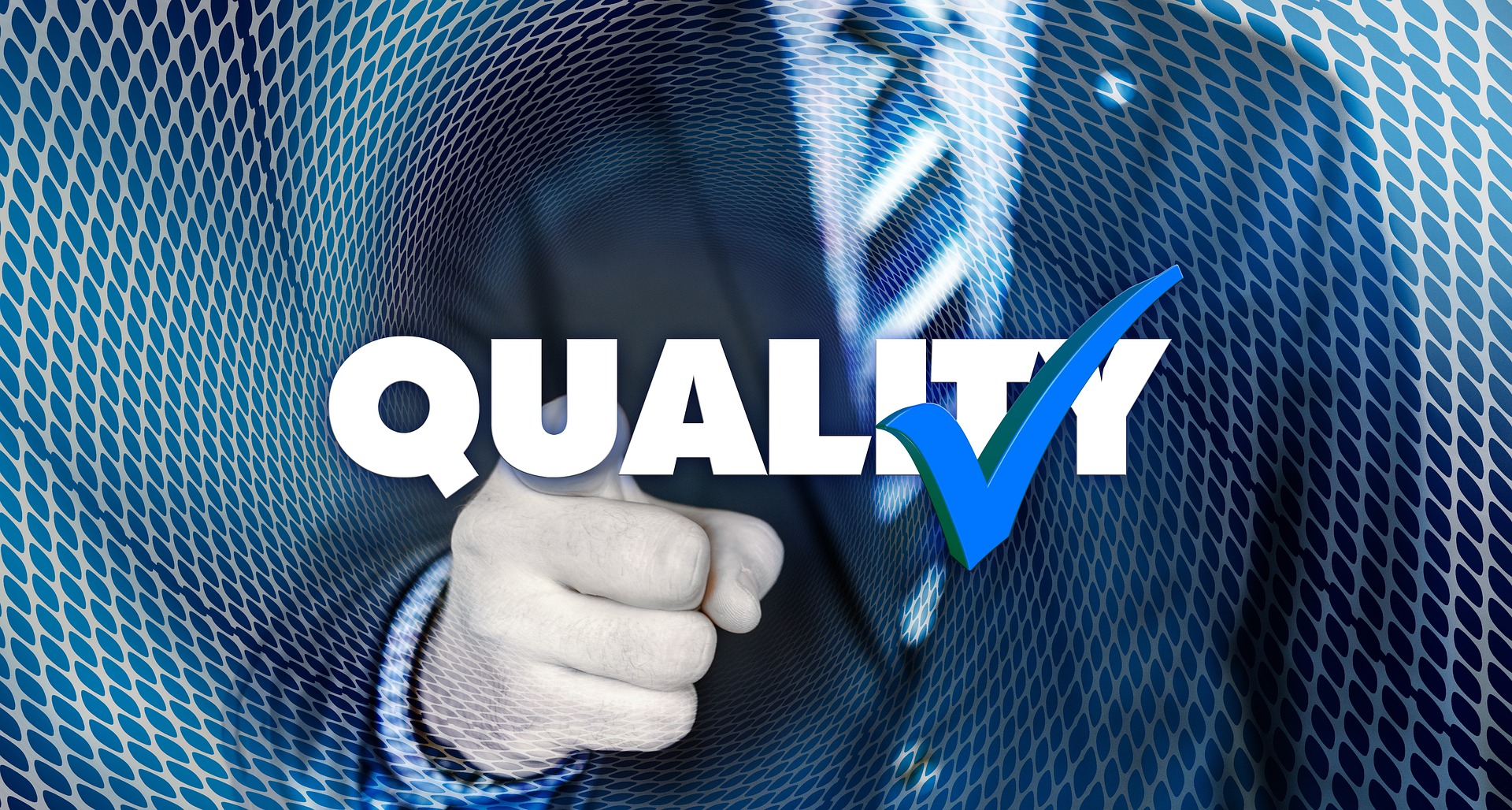
“Jidoka” è un termine giapponese, nato in casa Toyota, che indica e definisce un metodo fondamentale della Lean Manufacturing: la capacità di assicurare un flusso continuo attraverso la possibilità di bloccare le macchine in presenza di anomalie e/o difetti di produzione, garantendo allo stesso tempo un elevato standard qualitativo.
Cenni storici
La prima applicazione di questo metodo, ancora in embrione, avvenne nel 1896, ad opera di Sakichi Toyoda, futuro fondatore della Toyota Motor Company. Esso consisteva in un dispositivo molto semplice in grado di bloccare automaticamente un telaio in funzione nel caso in cui il filo si fosse spezzato. Individuato il filo spezzato, il dispositivo interrompeva la lavorazione segnalando l’anomalia in modo da non generare difetti di produzione; a quel punto interveniva l’operatore con la risoluzione del guasto e il ripristino delle operazioni di lavoro.
Il metodo
“Jidoka” si può tradurre con “automazione con intervento/tocco umano” che alcuni hanno pensato di tradurre, in maniera più specifica, coniando il termine “autonomazione”, ad indicare proprio un automatismo (del macchinario del caso) “con un tocco di umanità”.
La terminologia utilizzata è importante per capire il pensiero e l’intenzione di casa Toyota nello sviluppare Jidoka: la presenza umana, di concerto con meccanismi di bloccaggio, è fondamentale all’interno di ogni processo produttivo nel momento in cui qualcosa non dovesse funzionare. Ciò garantisce il pieno controllo lungo tutta la linea e la riduzione massima di ogni tipo di errore e difetto: il termine “autonomazione” è di fatto l’insieme dei termini “automazione” e “autonomia”.
Oggi il metodo si avvale di sensori di bloccaggio posti sui macchinari affinché possano interrompere il flusso in presenza di malfunzionamento e questo automatismo genera capacità di intervento in grado, con il tempo, di ridurre via via sempre più anomalie e scarti.
Affinché l’operatore possa intervenire in maniera adeguata, però, è necessario che egli venga formato per affrontare ogni eventualità e ridurre sempre più anche i tempi di risoluzione.
Le cause più frequenti di errore sono:
- Procedure operative inappropriate
- Materiali difettosi
- Eccessiva variabilità del modus operandi
- Errori umani e/o malfunzionamenti delle macchine
Di conseguenza le eventualità su cui un operatore deve essere preparato possono essere di varia natura:
- Problema qualitativo
- Problema di sicurezza
- Problema inerente alla strumentazione utilizzata
- Sovrapproduzione o mancanza di pezzi
I vantaggi di Jidoka
Applicare il metodo Jidoka alla propria produzione reca diversi vantaggi:
- Rilevazione dei problemi e loro tempestiva risoluzione
- Riduzione dei tempi di controllo qualità dovuti proprio alla capacità di individuazione dei problemi
- Protezione delle macchine da eventuale malfunzionamento dovuto a un problema non riscontrato
- Individuazione tempestiva delle anomalie tecniche così da rilevarne più facilmente le cause.
Il metodo Jidoka garantisce miglioramento continuo sulla base di un monitoraggio costante e di elevati standard qualitativi supportati e resi possibili, a loro volta, da adeguata preparazione.