SMED
L’acronimo SMED (Single Minute Exchange of Die) indica un’importante tecnica della Lean Production volta a ridurre i tempi di set up, cioè di preparazione di una macchina da un ciclo produttivo al successivo, cercando di arrivare a tempistiche di attrezzaggio inferiori ai 10 minuti.
Storia
I primi esempi di sistematizzazione e applicazione della tecnica SMED, si ebbero in Giappone, all’interno degli stabilimenti della Toyota, come ben sappiamo, fucine di sperimentazione e ideazione della Lean Production. Protagonista del percorso l’ingegner Shigeo Shingō. I casi in cui si imbatté l’ingegnere si manifestarono tra gli anni ’50 e gli anni ’70: il primo riguardò la presunta incapacità di tre presse, all’interno dello stabilimento Toyota, di soddisfare le richieste di produzione del mercato, tanto da far pensare all’acquisto di una quarta macchina. Shingō chiese di osservare attentamente l’intero processo di lavoro delle presse e, al termine della sua analisi, capì che il collo di bottiglia era dovuto all’inutilizzo delle presse alla loro massima capacità produttiva. Individuò e separò le operazioni che potevano e dovevano essere fatte a macchina ferma da quelle che invece potevano essere fatte a macchina funzionante e, in questo modo, ridusse di circa il 50% il tempo di set up non a valore aggiunto. Successivamente, sempre all’interno di uno stabilimento Toyota, si fece tesoro dell’esperienza precedente per ridurre i tempi di set up, classificando in maniera rigorosa le operazioni di set up interno e le operazioni di set up esterno e, una volta analizzati attentamente, si poté procedere con fasi di aggiustamento e miglioramento.
Le fasi dello SMED
Dall’esperienza Toyota in poi, dunque, lo scopo della tecnica SMED si riassume nella necessità di ottenere un Quick ChangeOver, cioè un ridottissimo tempo di passaggio da un tipo di produzione a un’altra, sul medesimo impianto e, dunque, nel drastico abbattimento dei tempi di attrezzaggio macchina, soprattutto di quelli destinati alla macchina ferma, non a valore aggiunto e dunque non produttivi.
Le fasi principali di applicazione della tecnica SMED sono 4:
- Analisi accurata del processo: è la fase dell’osservazione e raccolta dati per esaminare attentamente il ciclo produttivo. Utili a questo fine possono essere filmati, foto, Spaghetti chart (per monitorare gli spostamenti e i movimenti degli operatori), diagramma di Gnatt (per monitorare l’andamento delle attività dell’intero processo), e altri validi strumenti per ottenere un quadro il più possibile chiaro di ciò che avviene e come avviene.
- Individuazione delle operazioni IED (attività interne al fermo macchina) e operazioni OED (attività esterne al fermo macchina): classificando in maniera inequivocabile (e di conseguenza separandole) quelle che appartengono a uno stato e quelle che appartengono all’altro.
- Trasformazioni del maggior numero possibile di IED in OED: è molto importante riuscire a individuare le attività che possono essere svolte a macchina funzionante (OED, attività esterne al fermo macchina) perché in questo modo si riduce, in maniera significativa, il tempo non produttivo di un impianto.
- Miglioramento e, ove possibile, standardizzazione delle operazioni IED e OED: una volta individuate le attività, attribuendo ogni operazione al momento opportuno, è buona norma stabilire il giusto procedere rendendo sistemiche tutte le fasi riprogettate.
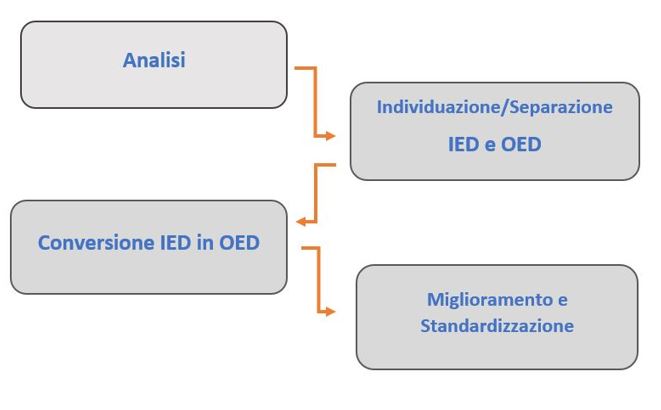
I vantaggi dello SMED
Adottare la tecnica SMED vuol dire ottenere importanti risultati:
- Maggiore flessibilità, garantita dal miglioramento delle fasi di set up
- Riduzione importante delle fasi di set up
- Più produttività in tempi minori
- Maggiore soddisfazione del cliente
- Riduzione degli eccessi di produzione, dovuti a un controllo maggiore delle operazioni e dell’intero processo
- Miglioramento del lavoro degli operatori, dovuto a una precisa razionalizzazione e una corretta gestione del tempo e delle mansioni.
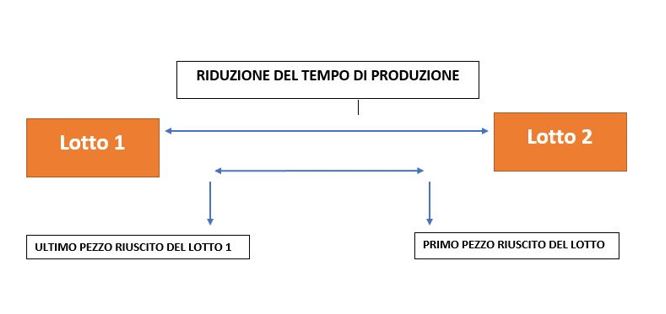