TPM
Con l’acronimo TPM si definisce il Total Productive Maintenance (Manutenzione Produttiva Totale), un approccio produttivo sistematizzato, all’interno della logica Lean, con l’obiettivo di raggiungere massima efficienza attraverso elevati standard di manutenzione di tutto l’apparato aziendale.
Prendendo direttamente spunto dal metodo Lean delle 5S, attraverso la cui standardizzazione di procedure precise si raggiunge lo scopo di ottimizzare risorse, spazi, tempi e processi produttivi, anche il TPM prevede una dettagliata prassi periodica al fine di rendere sistemici interventi di manutenzione preventiva, predittiva, autonoma e migliorativa ed evitare interruzioni dovute a trascuratezza e incuria, sprechi di tempo, scarti produttivi e conseguente diminuzione dei livelli qualitativi.
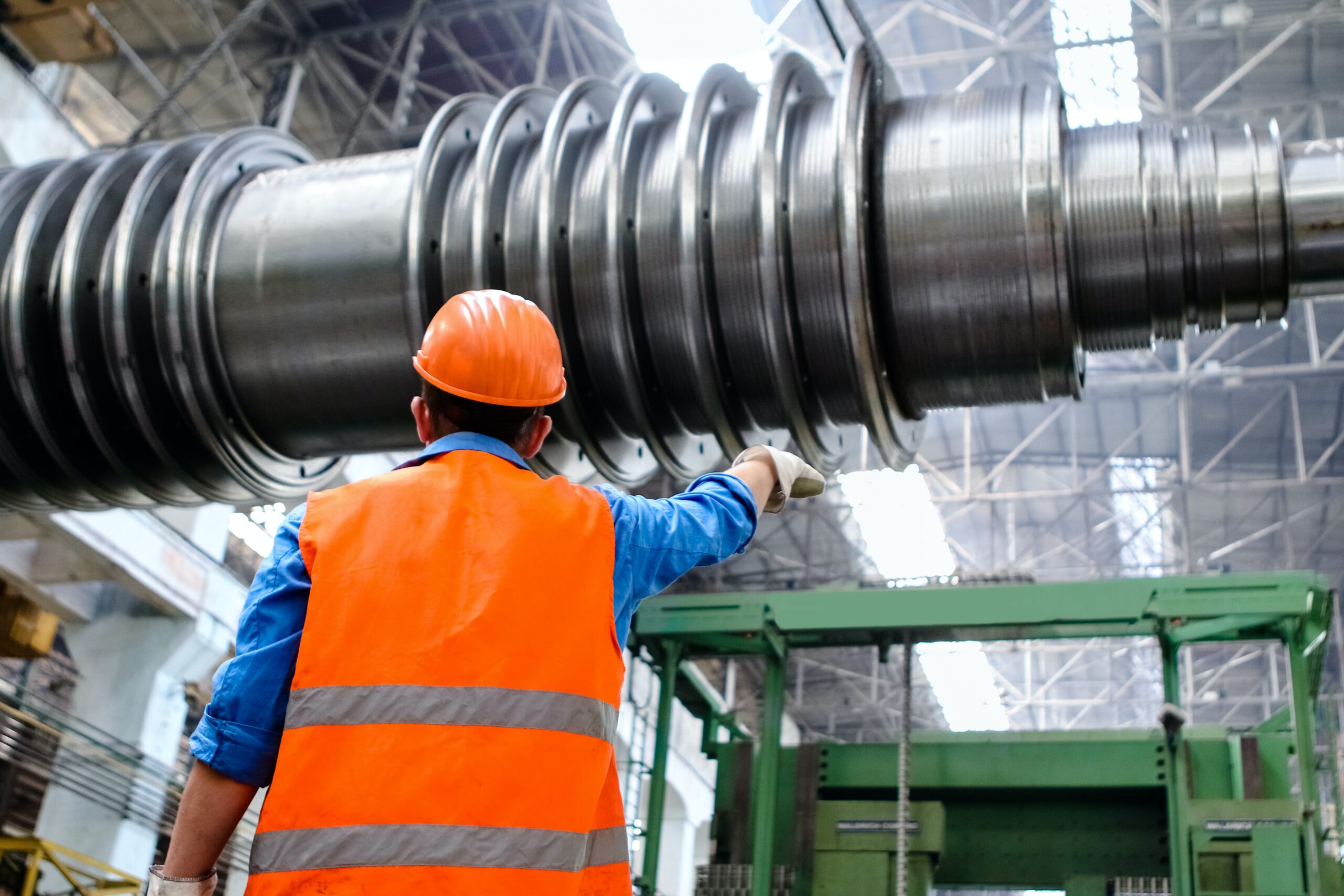
Storia
Come diversi altri strumenti, approcci e metodologie derivanti dalla Lean Production, anche il TPM nasce in Giappone e in casa Toyota, il cui allora direttore tecnico Seiichi Nakajima, si dedica alle teorie e pratiche americane di affidabilità, manutenibilità, life cycle cost e manutenzione preventiva all’interno delle fabbriche. Appassionatosi all’argomento lo struttura in un libro del 1984, Total Productive Maintanance, in cui ne spiega principi, benefici e obiettivi. Diventato poi consulente della Japan Management Association (JMA) e del Japan Institute of Plant Maintenance (JIPM) si impegnerà per far conoscere in tutto il Paese e anche all’estero, le tecniche attuative e a diffonderne l’adozione.
La validità delle stesse viene confermata dall’istituzione di un premio a lui dedicato, il Nakajima Prize, che sottolinea l’alto grado di competitività che gli elementi del sistema, raccolti in una solida visione organica, apportano alle aziende.
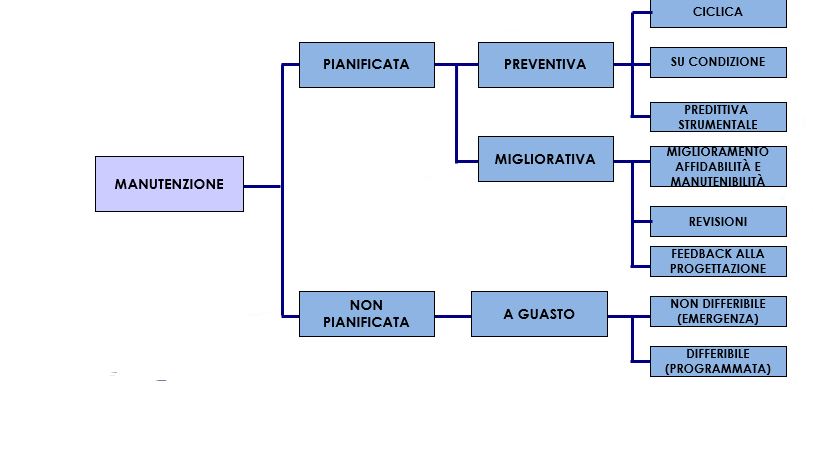
Quali sono i passi da seguire?
- Manutenzione Autonoma e Preventiva: introdurre attività di miglioramento per aumentare efficienza degli impianti e delle attrezzature, quali piccoli interventi di manutenzione ordinaria, (pulizia periodica, controllo componenti, lubrificazione ecc…) che possono essere svolti direttamente dall’operatore addetto alla macchina o all’impianto in questione in modo da rendere autonoma questa parte fondamentale di prevenzione guasti e interruzioni ad esso dovuti, e facendo in modo che i tecnici professionisti della manutenzione possano invece dedicarsi ad attività a maggior valore e necessità.
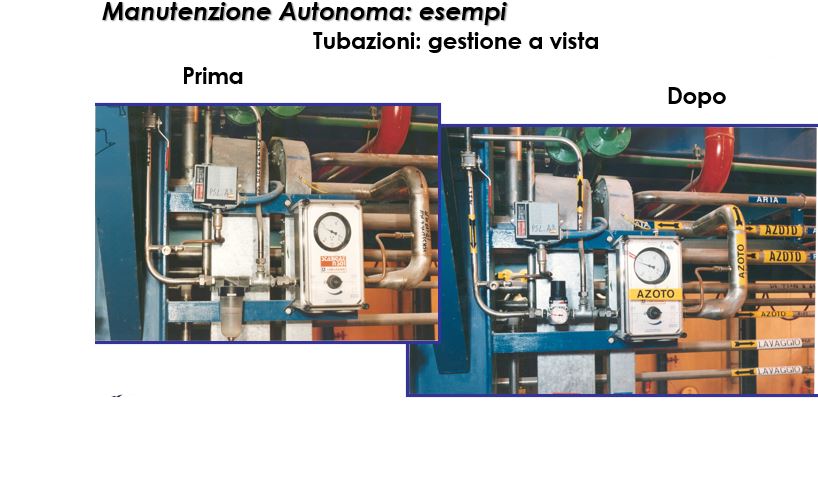
- Manutenzione Programmata e manutenzione predittiva: attuare sistemi di interventi programmati, basati sulla raccolta dei dati di performance dei vari macchinari e dei vari impianti, in modo da avere un’idea di sorta, dietro analisi e valutazioni statistiche, su ciò che è il ciclo di vita della macchina e del suo funzionamento. In questo modo si possono anche modificare i vari interventi e ricalibrarli sulla base dei risultati d’osservazione.
- Miglioramento della Qualità: monitorare la qualità dei prodotti ha l’obiettivo di evitare il più possibile errori di produzione, come oggetti non conformi agli standard. Gli scarti di produzione rivelano inefficienza di impianti e processi, determinando spesso perdite di produzione e di tempo dovute alla rilavorazione. Uno strumento di misurazione molto valido in questo senso è l’Overall Equipment Effectiveness (OEE), cioè la misura di efficacia di un impianto che raccoglie in sé tre dimensioni importanti: la Disponibilità, l’Efficienza/Produttività e il tasso di Qualità di un impianto.
La Disponibilità è il rapporto tra Tempo Operativo e Tempo Disponibile per la Produzione, dove come Tempo Disponibile si intende il tempo totale disponibile della macchina nell’arco di un anno, a parte le chiusure pianificate, e con Tempo Operativo si intende, invece, il Tempo Disponibile meno il Tempo in cu la macchina è occupata da attività non pianificate.
La Produttività è data dalla differenza tra Tempo Operativo Netto e Tempo Operativo, già definito. Il Tempo Operativo Netto è dato dal Tempo Operativo meno il tempo dovuto alle inefficienze produttive.
La Qualità è il rapporto tra il Tempo Operativo a Valore e il Tempo Operativo Netto, già definito. Il Tempo Operativo a Valore è il Tempo Operativo Netto meno il tempo perso a causa di scarti di produzione, rilavorazioni ecc…, cioè a causa di difetti di qualità.
- Formazione: è importante che tutti collaborino al programma di efficientamento generale e che quindi ogni lavoratore sia interessato da percorsi formativi che lo rendano in grado di intervenire al momento opportuno.
- Partecipazione dell’amministrazione/management: l’impulso al nuovo mindset deve partire dal management e dall’amministrazione al fine di responsabilizzare il personale nel farsi carico di operazioni che potrebbero esulare dal loro compito principale.
- Ambiente e Sicurezza: creare un ambiente di lavoro sicuro è un altro aspetto fondamentale del TPM.
I Vantaggi del TPM e Finalità Operative
Seguendo il programma di attuazione del Total Productive Maintenance, i vantaggi sono facilmente immaginabili e possiamo cosi riassumerli:
- Uso più efficiente di impianti e attrezzature;
- Introduzione di una metodologia di manutenzione diffusa in tutta l’organizzazione e basata su osservazioni e dati, cioè sulla manutenzione predittiva;
- Stimolo alla partecipazione in fase di progettazione e sviluppo, produzione e manutenzione;
- Coinvolgimento del management e di tutti gli operatori;
- Promozione e miglioramento delle attività di manutenzione attraverso l’attività di team autonomi e specifici.
Le Finalità Operative sono invece le seguenti:
- Ridurre l’entità della causa di guasto (durata)
- Ridurre la frequenza di apparizione della causa (numero)
- Imparare a riconoscere ed eliminare le cause prima che si manifesti il guasto (prevenzione)
- Ridurre i costi totali dell’intervento (ottimizzazione del lead time di intervento).